I am using the driver as per website:
https://coeleveld.com/arduino-stepper-l298n/
With the code on this page everything works fine. I can not force this IC to work with B4R.
I looked at the library Stepper.cpp - Stepper library for Wiring/Arduino - Version 1.1.0 and it should be simple, but help always will be useful: D
https://coeleveld.com/arduino-stepper-l298n/
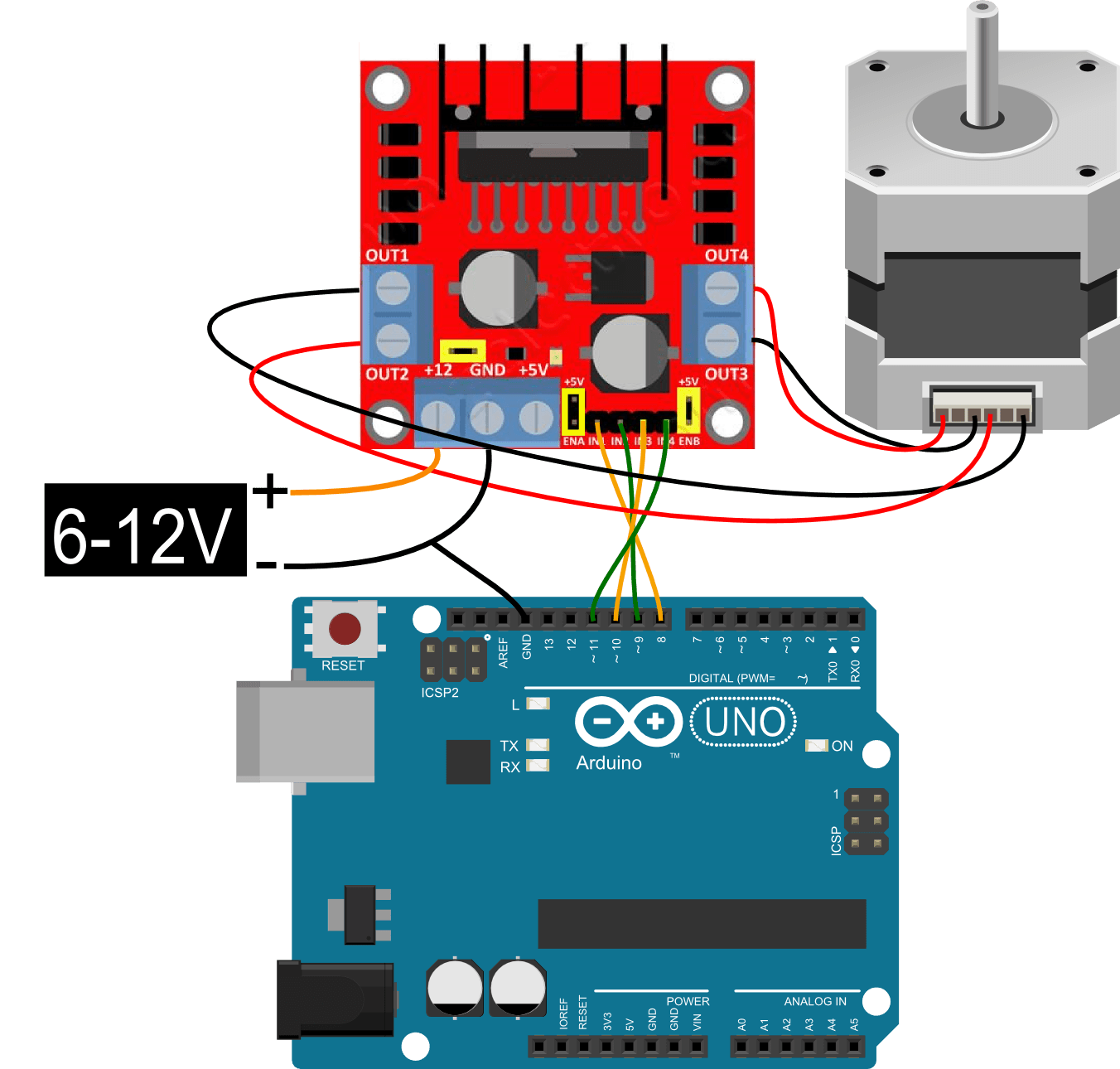
With the code on this page everything works fine. I can not force this IC to work with B4R.
B4X:
/*
Stepper Motor Control - one revolution
This program drives a unipolar or bipolar stepper motor.
The motor is attached to digital pins 8 - 11 of the Arduino.
The motor should revolve one revolution in one direction, then
one revolution in the other direction.
Created 11 Mar. 2007
Modified 30 Nov. 2009
by Tom Igoe
*/
#include <Stepper.h>
const int stepsPerRevolution = 200; // change this to fit the number of steps per revolution
// for your motor
// initialize the stepper library on pins 8 through 11:
Stepper myStepper(stepsPerRevolution, 8, 9, 10, 11);
void setup() {
// set the speed at 60 rpm:
myStepper.setSpeed(60);
// initialize the serial port:
Serial.begin(9600);
}
void loop() {
// step one revolution in one direction:
Serial.println("clockwise");
myStepper.step(stepsPerRevolution);
delay(500);
// step one revolution in the other direction:
Serial.println("counterclockwise");
myStepper.step(-stepsPerRevolution);
delay(500);
}
I looked at the library Stepper.cpp - Stepper library for Wiring/Arduino - Version 1.1.0 and it should be simple, but help always will be useful: D
Last edited: